E-Coating
Technically called Nano-Ceramic E-Coating, e-coating uses an electrical current to deposit transparent abrasion-resistant nano-sized ceramic particles onto the surface of the jewelry, creating a durable protective hypoallergenic and tarnish-resistant finish.
E-coated jewelry keeps the look, feel, and sound of the metal that is at their core.
Argentium silver is more tarnish-resistant than traditional sterling silver, but all natural uncoated silver reacts with the sulfur in the air and tarnishes over time. This e-coating helps to prevent this reaction.
The Process
Follow along as I apply a nano-ceramic e-coating to pieces in our collection.
E-coating is quite similar to metal plating, but it requires additional steps and needs additional tools like a curing oven and a magnetic stirrer.
Having meticulously cleaned jewelry is a must. My process starts with placing the pieces into a hot ultrasonic cleaner, followed by a thorough steam-cleaning, followed by an electro-cleaning bath.
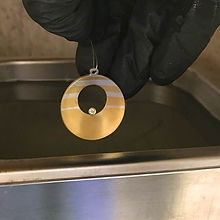
Ultrasonic Cleaning
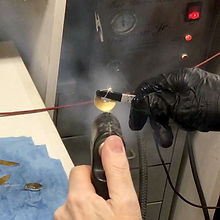
Steam Cleaning
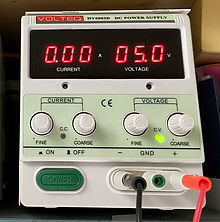
Rectifier set to 5 Volts

Electro Cleaning
The pieces are rinsed in distilled water, then placed into an acid-dip solution (which neutralizes the electro-cleaner), then rinsed again with distilled water.
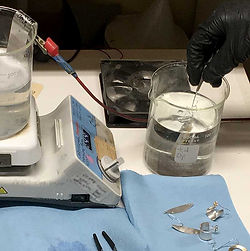
Acid Dipping
The jewelry needs to be completely dry before it can be electro-coated. Any moisture left on the pieces will cause the coating to develop bubbles. To dry them, I place them into an oven set to 180 degrees for 10 minutes.

The e-coating solution is filtered through a very fine mesh before each use. I also filter the surfactant (bubble remover), just to make sure there are no dust particles that could transfer onto the coating.

e-coating
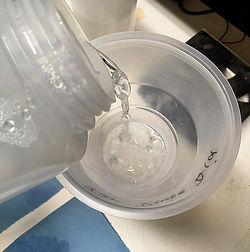
Surfactant
Next is the actual coating process. The rectifier is set to 60 Volt and the jewelry is dipped into the solution. The magnetic stirrer underneath the beaker agitates the solution, which helps the solution to reach recessed areas and with surface bubble removal.
After 20 seconds the jewelry is taken out, rinsed in two consecutive distilled water beakers, dipped into a surfactant liquid (which also helps to reduce potential bubbles), sprayed with compressed air to remove excess solution, and hung to dry.

Rectifier set to 60 Volts

Nano-ceramic e-coating
solution
The pieces dry until their milky-looking coating develops a sheen, then they are transferred into the oven (40 min at 270 degrees Fahrenheit) to cure the nano-ceramic e-coating. Then they are air-cooled to room temperature.



E-coated finished piece.